Blog
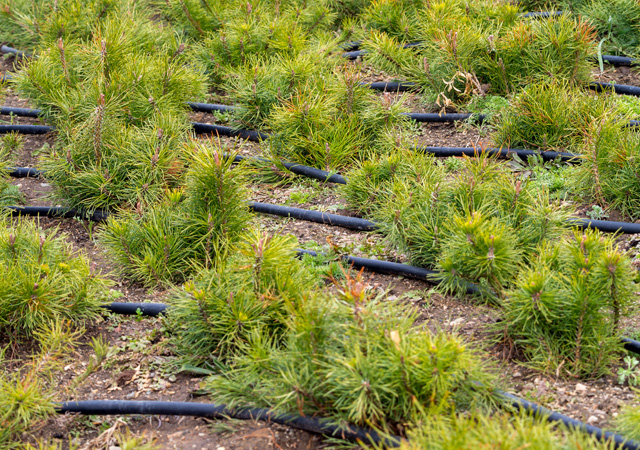
A New Era in Irrigation
Subsurface drip irrigation helps eliminate washout, evaporation By Lindsay Owens From “Growing In The Heartland” Magazine October 2015 LOOKING AT BILL Resler’s field of corn located just outside of Oaktown, one may not noticed much of anything out of the ordinary. The stalks are tall and adorned with ears of corn waiting to mature for harvest. The gentle sound of a pump running echoes in the background but you won’t
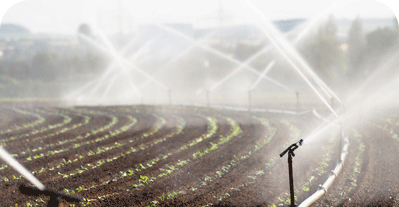
Winterization Using Air Blow Out
Introduction: In a freezing climate it is advisable to “winterize” the sprinkler system in order to avoid damage. Special attention should be given to removing water from the pipes, valves and sprinkler heads, before freezing occurs. This may be accomplished using three techniques; the manual drain valve method, the automatic drain valve system, or the air blow-out practice. This guide
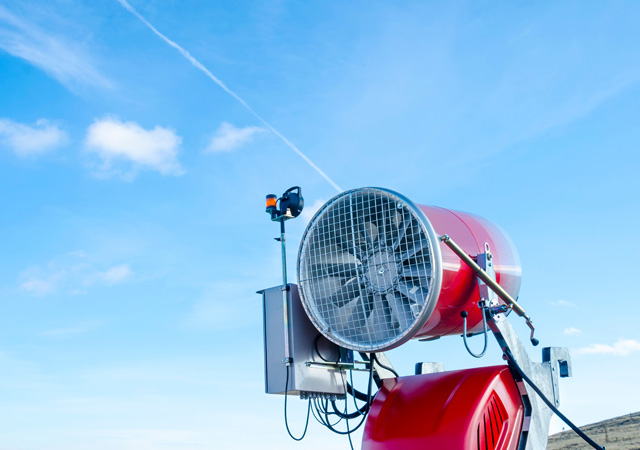
No More Airblast Spraying?
Goal is to perfect a Solid Set Canopy Delivery System for all sprays. Think of all the materials you put on your orchard through your airblast sprayer: Insecticides, fungicides, antibiotics, chemical thinners, plant growth regulators, sunburn protectants, foliar nutrients, anticracking agents. Now suppose that, instead of lugging them up and down the alleys in dozens of trips and thousands of
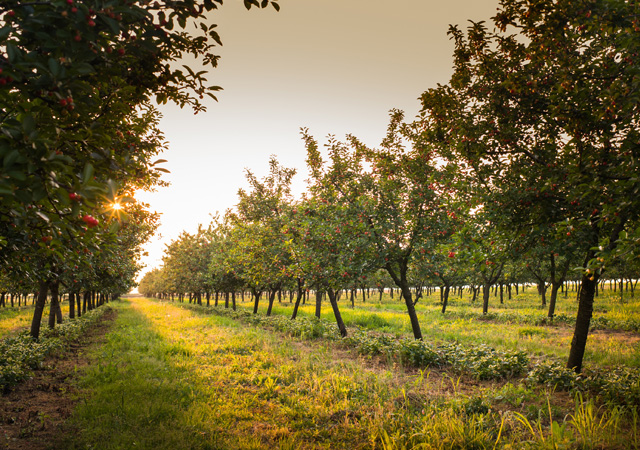
New Spray Concept Proves Feasible
A fixed-in-place orchard spraying system is fast becoming something to consider. If we had to irrigate orchards by pulling tanks of water down the alleys, would we do it? We do that now with pesticides and plant growth regulators, hauling loads of water with small amounts of chemicals in them, then blasting the mixtures into the trees. Only about a
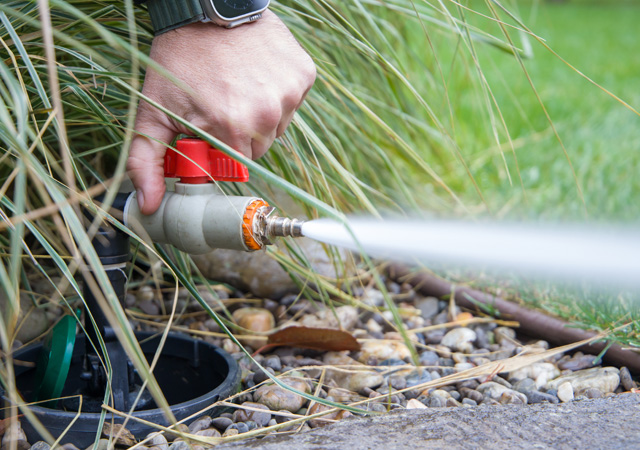
Performance Report – Solid-set Canopy Spray Delivery System
Solid-set canopy spray delivery system looks good in first year of tests. After a year of work, the team of researchers developing Solid-Set Canopy Delivery Systems has issued its first report—and the results look promising. Control of codling moth and mildew was “not quite as good” as airblast sprayer application, but acceptable, the report says. Coverage for most foliar inputs
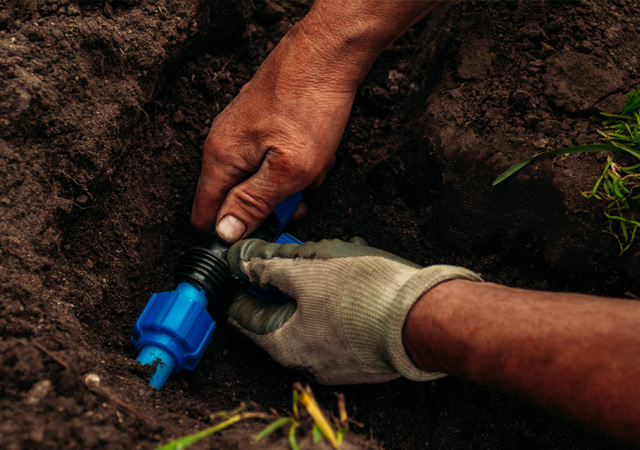
Underground Drip Irrigation Serves Two Purposes
Dispose of wastewater and irrigate trees. Water is plentiful in the fruit-growing area along Lake Michigan’s eastern shore, so it’s not scarcity that’s an issue. The problem is with some water that’s been made slightly dirty but is perfectly useful if handled right. That’s led some fruit growers and fruit processors to make double use of wastewater through subsurface trickle
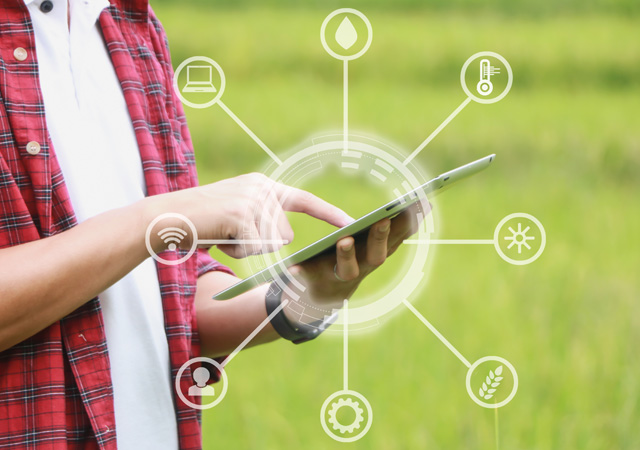
A-Mazing New Technology
Novel spraying system is incorporated into a maze built of rows of apple trees. One of the tree fruit industry’s newest technologies is making its debut—amazingly—in a five-acre maze shaped like an apple and created, not out of corn, as most mazes are, but of apple trees. Mazes are popular attractions. But how would one manage an orchard with all
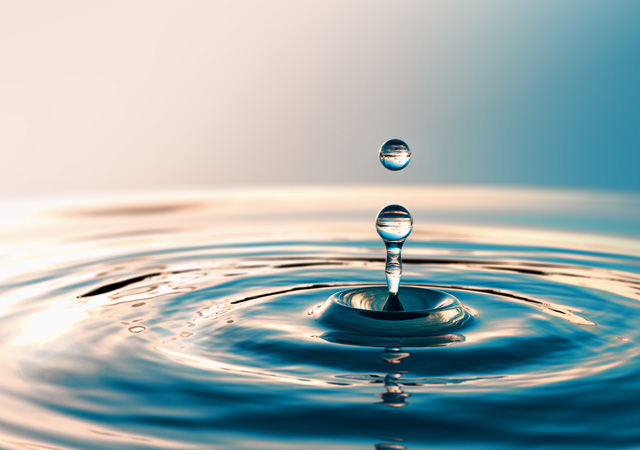
10 Amazing Facts About Water
1- There is the same amount of water on earth today as when the earth was formed. (Ewww factor or cool factor?) The water coming out of your faucet today could contain molecules ancient humans used thousands of years ago. 2- Need some cocktail conversation for the World Ag Expo? Frozen water is lighter than water by about 9%, which is why ice
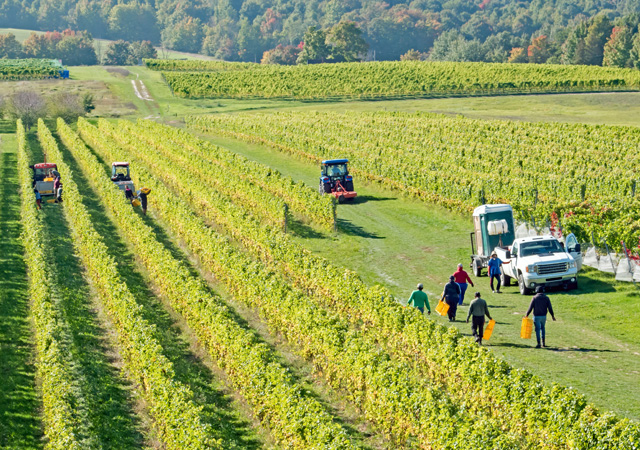
Hartford Grower Chairs Michigan Ag
The legend of High Acres Fruit Farm in Hartford has a new milestone with the election this week of a member of the Meachum family to the chairmanship of the Michigan Commission of Agriculture & Rural Development. Trever Meachum is Production Manager for High Acres Fruit Farm, and his election Wednesday has been announced by the Michigan Department of Agriculture
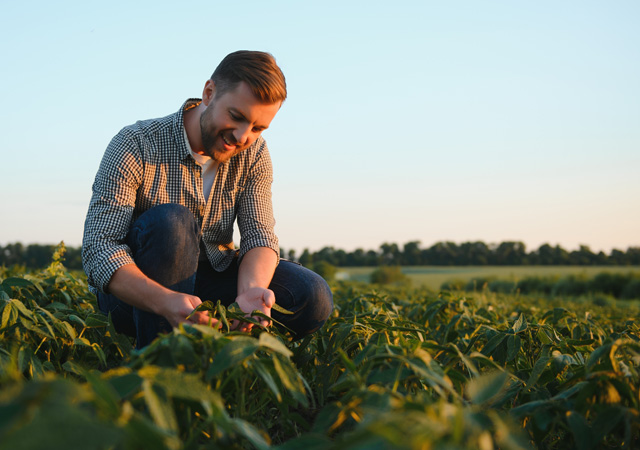
Young Grower, Packer Running At Full Speed
On a hot day in late July, Jason Kuehnle, a young, aggressive vegetable grower and packer was busy hustling. He was in the midst of supervising and working alongside packing employees who were boxing bell peppers for shipments all over the Midwest and beyond. Kuehnle, 28, learned early and fast that aligning yourself with the right people is the key
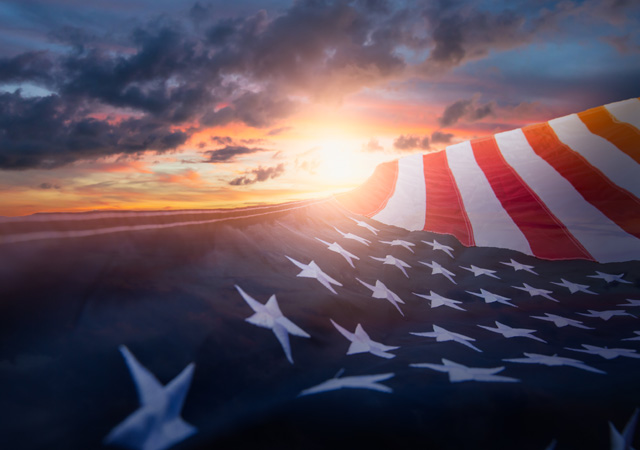
TRICKL-EEZ GOES WITH THE FLOW
ST. JOSEPH – John Nye never got away from the family farm in Royalton Township, but the products made by his company are helping grow food in Peru, Saudi Arabia, Canada and Mexico, as well as all over the United States. Nye and his wife, Sandra, own the TRICKL-EEZ Company. “We started in 1972 and incorporated in 1973,” Sandra said, thus
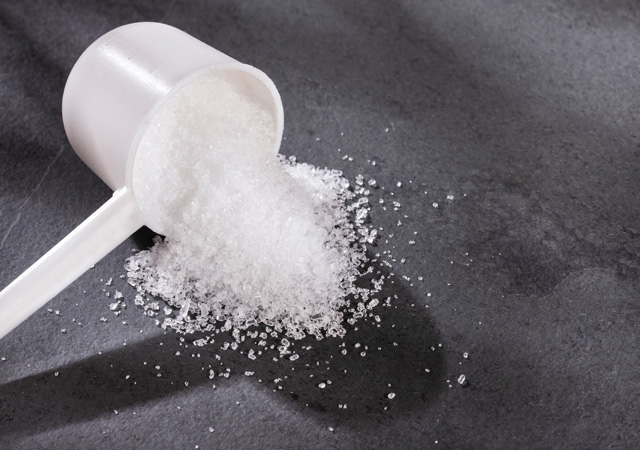
CHLORINE TREATMENT TO CONTROL ALGAE AND ORGANIC BUILDUP
Chlorine treatment for controlling algae, and/ or other organic buildup in drip tubing and emitters. Chlorine is an effective treatment to kill or control algae and other organic buildup and is commonly used as an additive in municipal drinking water, swimming pools, hot tubs, etc. In small quantities there is minimal harm to humans, animals or plants. Quantities of chlorine exceeding